Laser cladding 3D printing (that is, laser cladding molding) technology uses a CAD software to make a part model without a mold. After programming, the computer scans the workpiece with a beam of laser light to melt the metal powder on the workpiece and fuse layers. Together and stacked, eventually forming a dense metal part. This technology can form metal parts in one step, while dense metal parts formed after intelligent process control are nearly net-shaped, and almost no subsequent processing is required to truly achieve rapid and cladding 3D printing of metal parts.
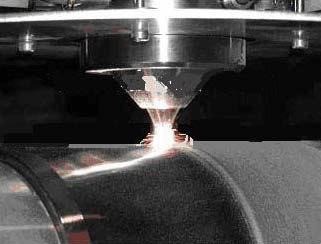
It provides prototype parts that can be used as product development and design concepts and performance testing samples, and can also be used directly as functional parts. Laser cladding molding technology can greatly reduce the time from product development to the market, and greatly reduce the cost of product development. In particular, it can make product manufacturing faster, more flexible, personalized, and more diverse. It has unparalleled advantages in single-piece small-volume production, which facilitates network manufacturing and is also suitable for the trend of economic globalization. It can more efficiently manufacture high-precision parts in civilian fields such as new automobile manufacturing, medical treatment, and instrumentation. The military industry can better manufacture high-performance special parts, especially gradient functional materials and super-hard materials that were extremely difficult to process in the past, and it can also quickly manufacture intermetallic material parts, so this technology has a broad application prospect.
At present, laser cladding 3D printed parts still have some shortcomings, such as poor quality stability, not meeting the user’s required accuracy and roughness, and further processing of the part is required. Therefore, the limitations of this technology have led to its failure. Better use in production. The reasons for the poor quality stability of the part are: during the process of making the part, some process parameters will fluctuate, and the shape and size of the cladding band formed in some parts of the part will not meet expectations; it will also expand when the cladding is in progress The defects that have been formed make the protruding places more protruding, the subsided places more sinking, the thicker places thicker, and the thinner places thinner. In this way, the roughness and accuracy of the parts do not meet the expectations, and the most serious part is that the parts cannot be formed.

Laser cladding means that the selected coating material is placed on the surface of the substrate to be cladding in different ways, and is irradiated with a thin layer of the surface of the substrate at the same time by laser irradiation. After rapid solidification, the degree of dilution is extremely low. The surface coating which is metallurgically combined with the substrate can significantly improve the abrasion resistance, corrosion resistance, heat resistance, oxidation resistance and electrical characteristics of the surface of the substrate, so as to achieve the purpose of surface modification or repair. The performance requirements have saved a lot of valuable elements.
Compared with surfacing, spray coating, electroplating and vapor deposition, laser cladding has the characteristics of small dilution, dense structure, good coating and substrate combination, suitable for cladding materials, large particle size and content change, etc. Therefore, laser cladding technology The application prospect is very broad.
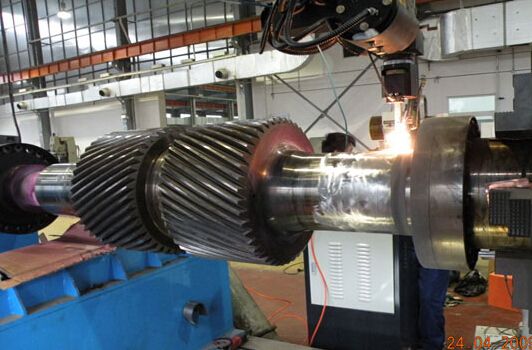
From the current application of laser cladding, it is mainly used in three aspects:
First, the surface modification of materials, such as gas turbine blades, rolls, gears, etc .;
Second, the surface repair of products, such as rotors, molds, etc. Relevant data shows that the strength of the repaired parts can reach more than 90% of the original strength, and the repair cost is less than 1/5 of the replacement price. More importantly, it shortens the maintenance time and solves the continuous and reliable operation of major complete sets of equipment in large enterprises. The problem of rapid repair of the rotating parts that must be solved. In addition, laser cladding of super wear-resistant anti-corrosion alloy on the surface of key components can greatly improve the service life of components without deforming the surface of the component; laser cladding treatment on the surface of the mold not only improves the strength of the mold, but also Can reduce 2/3 of manufacturing cost and shorten 4/5 of manufacturing cycle.

Third, rapid prototyping. Use the metal powder layer-by-layer sintering and stacking to quickly make the model. The technology of rapidly manufacturing parts using laser welding technology is also called LENS (LaserEngineeredNetShaping), DLF (DirectLaserFabrication), DMD ( DirectMetalDeposition), LC (LaserConsolidation), etc.
Cladding materials: At present, laser cladding materials that are widely used are mainly nickel-based, cobalt-based, iron-based alloys, tungsten carbide composites, ceramics and other materials. Among them, nickel-based materials are the most widely used, which is cheaper than cobalt-based materials.
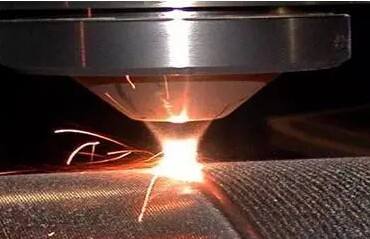
Compared with the commonly used overlay welding, thermal spraying and plasma spray welding, laser cladding has the following advantages:
High bonding strength between substrate and cladding layer, small heat-affected zone, high efficiency of small cladding layer and substrate grain size, saving expensive materials, preparation of gradient functional materials, good controllability of laser cladding technology, easy to achieve automatic control, coating Layer quality is stable.
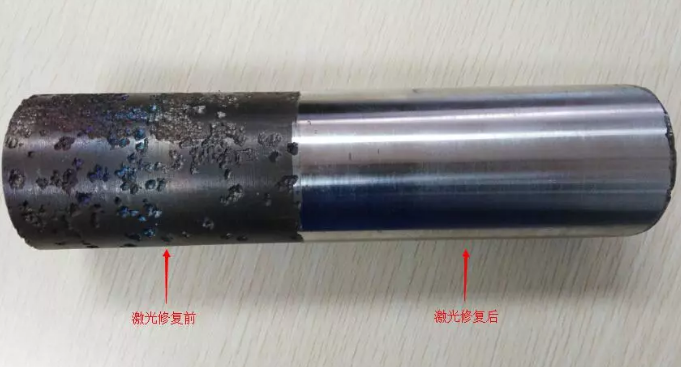
The ultra-high-speed cladding technology uses synchronous powder feeding and feeding to use a high-energy density beam to melt the additive material and the surface of the base material moving at a high rate at the same time, and quickly solidify to form a very low dilution rate. The cladding layer greatly improves the cladding rate and significantly improves the process characteristics of the surface of the base material such as wear resistance, corrosion resistance, heat resistance, and oxidation resistance.
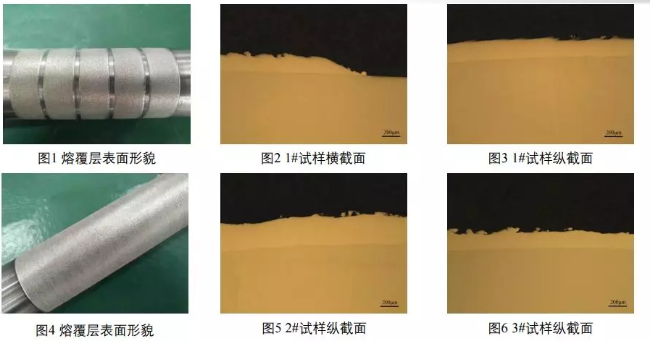
It is suitable for parts in electric power, aviation, aerospace, weaponry, nuclear industry, and automotive industry that need to improve performance. According to the working conditions of the workpiece, metal or non-metals of various design components are cladding to prepare a heat-resistant, wear-resistant, corrosion-resistant, oxidation-resistant, fatigue-resistant or surface coating with optical, electrical and magnetic characteristics.
Ultra-high-speed laser cladding technology is a new technology with high economic benefits. It can prepare high-performance alloy surfaces on metal substrates without affecting the properties of the substrate, reducing costs and saving precious and rare metal materials. Therefore, the world Research and application of laser cladding technology in all the industrial advanced countries in the country are very important.
Cladding process: Laser cladding can be roughly divided into two categories according to the cladding material supply method, namely preset laser cladding and synchronous laser cladding.
Pre-set laser cladding is to place the cladding material on the cladding part of the substrate surface in advance, and then scan and melt it with laser beam irradiation. The cladding material is added in the form of powder, wire, and plate. Often used.

Synchronous laser cladding sends the cladding material directly into the laser beam, so that feeding and cladding are completed at the same time. The cladding material is mainly fed in the form of powder, and some also use wire or plate for synchronous feeding.
The main process flow of preset laser cladding is: pretreatment of substrate cladding surface — preset cladding material — preheat — laser melting — post heat treatment.
The main process flow of synchronous laser cladding is: surface pretreatment of substrate cladding — feeding laser melting — post-heat treatment.
According to the process flow, the processes related to laser cladding are mainly substrate surface pretreatment methods, cladding material feeding methods, preheating and post-heat treatment.