[Rayclass | Rui Class] No. 7: Breaking the Welding Difficulties of Aluminum Alloys-Laser Welding Process of Rail Trains
Friends who are concerned about our solutions in the welding field must not miss these two good articles recently:
We received a message asking:
Is there a welding solution for other materials?
Is there a real use case other than a test scenario?
Nowadays
We not only bring 6000W fiber laser
Solutions for welding aluminum alloys
and
More than just theory and experiment
Is a case of real application to train bodies
Ado
[Rayclass | Rui Class] No. 7
Talk now

With the continuous expansion of the scale of cities in our country, the rapid development of urban economy and the continuous improvement of modernization level, rail transit has become the best choice for public transportation systems in cities in China.
As an important tool for transporting passengers, the level of train manufacturing directly affects the development scale and speed of rail transit, and various advanced technologies have also been widely used in the manufacture of rail transit vehicles. Among them, the laser welding technology has a unique advantage in the manufacturing process of stainless steel car bodies, and it will definitely become a weapon for welding in the future.
The weight reduction of rail trains, especially high-speed rail and double-decker buses and subway trains, is the central issue in the modernization of rail transport. The large-scale use of aluminum alloy materials is the most effective way to improve vehicle weight reduction.
In order to meet the requirements of vehicle design, aluminum alloy materials are widely used in the manufacture of high-speed rail and subway.
But did you know that aluminum alloys are recognized as “difficult to weld” materials:
○ Weld joints are softened severely and the strength is reduced;
○ There are many pores in the weld and it is easy to crack;
○ The weld seam is easy to collapse, causing serious undercuts.
Since there are so many defects in aluminum alloy welding,
Do we have nothing to do?
During the manufacturing process of rail transit, there are strict requirements for laser welding welds. It is necessary to meet the laser welding standard “GB / T 22085.2-2008 / ISO 13919-2,2001”, which has the following aspects:
○ The size and number of air holes in the weld;
○ Welding molding-Yu Gao, collapse, undercut, etc.
It is difficult to meet the requirements using conventional single laser welding, especially for welding relatively thick 3-6mm aluminum alloy materials. In order to solve this problem, two existing schemes can be recommended to everyone.
Option 1: Laser Filler Welding
Basic equipment : RFL-C6000 laser, welding head, wire feeder, soft gun tip
Welding platform : (as shown below)
Plate thickness (mm) Laser power (w) Welding speed (m / min) Wire feeding speed (m / min)
Welding effect :
3mm aluminum alloy butt joint
4mm aluminum alloy butt joint
Option 2: Laser-arc hybrid welding
Basic equipment : RFL-C6000 laser, welding head, welding machine, wire feeder, hard gun head
Welding platform : (as shown below)
Plate thickness (mm) Laser power (w) Welding speed (m / min) Wire feeding speed (m / min)
Welding effect :
5mm aluminum alloy butt joint
6mm aluminum alloy butt joint
Both application solutions have been installed in our end customer (a railroad equipment manufacturing company in Qingdao). One of the products produced is a locomotive component. As shown in the figure below, good welding results have been achieved.
Compare the two options
Different applications
For welding materials of the same thickness, laser filler wire welding requires higher laser power, but can obtain higher welding efficiency, which has greater advantages when welding thinner plates; for RFL-C6000 lasers, laser filler wire welding The recommended thickness of aluminum alloy is 1 ~ 4mm;
Laser-arc hybrid welding has arc heat involved in the welding process, so the same weld penetration can be obtained with a lower laser power. However, in order to ensure the formation of the weld, the welding speed cannot be too fast, and the equipment cost will be certain. However, the laser-arc hybrid welding can complete the welding of thicker aluminum alloys. For the RFL-C6000 laser, the recommended thickness of laser-arc hybrid aluminum alloys is 4-7mm.
Compared with traditional arc welding and resistance welding, laser welding has the advantages of fast welding speed, high production efficiency, narrow welds and heat affected zones, and small welding deformation. Therefore, the research on the laser welding technology of stainless steel body in the field of rail transit has received more and more attention.
In addition to the “face problem” of the car body, in the future we will also use laser welding to solve the processing and manufacturing of key components of rail transit. We also look forward to using laser technology to help the rapid development of China’s rail transit and the entire manufacturing industry in the future.
Winter is coming
Most parts of the country are about to enter “subzero”
[Rayclass | Rui Class]
Also remind all laser users here
Beware of laser freeze protection in extreme weather
(Click on the picture for antifreeze knowledge)
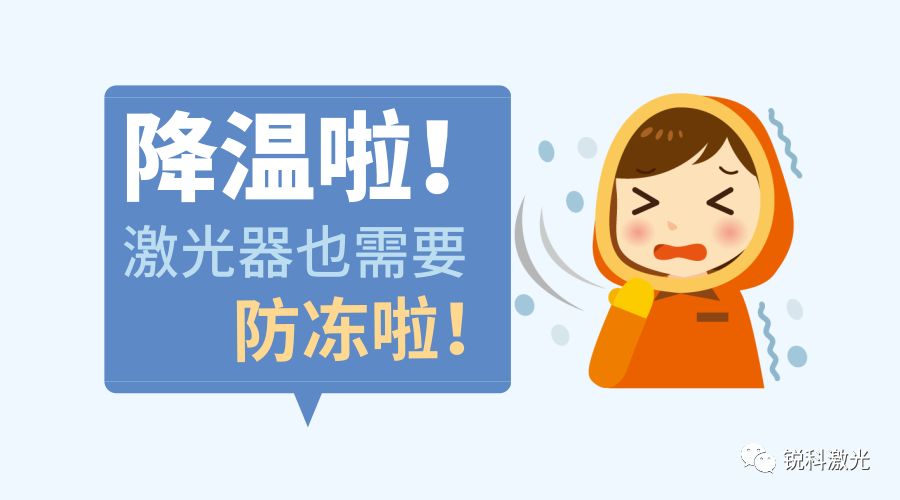